Force Measurement Error – Time Interval Between Two Successive Loadings
Has anyone ever wondered if there is a difference in calibration results if the time interval between two successive loadings is changed? Is faster better and does it matter if the calibration takes 10 minutes on an automated machine pictured in Figure 2 below, or two to three hours at NIST or a comparable lab with deadweight calibration systems?
Figure 1 Morehouse 120,000 lbf deadweight machine
Having five deadweight machines and the ability to automate when the reading is captured, Morehouse decided to do a test on a standard shear web load cell and record the results. We will get to those results below, however before we discuss those results, let’s review what the two most recognized force standards say about the time interval between calibrations.
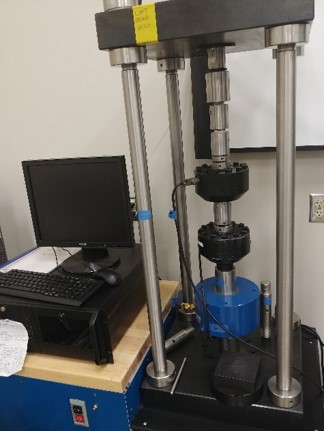
ISO 376 section 7.4.3 Loading conditions states, “The time interval between two successive loadings shall be as uniform as possible, and no reading shall be taken within 30 seconds of the start of the force change.”
ASTM E74 section 7.4.1 states - “After exercising, apply the calibration forces, approaching each force from a lesser force. Forces shall be applied and removed slowly and smoothly without inducing shock or vibration to the force-measuring instrument. The time interval between two successive loadings or removals of forces and in obtaining readings from the force-measuring instrument shall be as uniform as possible. If a calibration force is to be followed by another calibration force of lesser magnitude, reduce the applied force on the force-measuring instrument to zero before applying the second calibration force.”
While ISO 376 gives clear guidance on the timing, ASTM E74 only references as uniform as possible. Our question is, what would happen to the output of a shear web load cell if we varied the timing but kept it as uniform as possible and compared the ISO 376 requirement of 30 seconds versus 6 seconds? After all, if we can take readings at 6 seconds instead of 30 and we take an average of 66 calibration points, we could save 26.4 minutes for every calibration we perform. We have about 600 minutes in our working day and can do about 4 total tension and compression ASTM E74 calibrations per deadweight machine. If we lower the dwell time, we could potentially do 20 % more calibrations daily. However, ISO 376 calibrations would still require 30 seconds.
Figure 3 Morehouse Shear Web Load Cell
A controlled test was done using automated data capture software. The UUT (Unit Under Test) was not moved, and 2 series of readings were taken at the same position, with one test of 2 series of readings being performed with a delay before the read setting of 6 seconds and a second test being performed at a delay before the read of 30 seconds. This timing was set in our data capture software, and we assumed the computer's internal time was more accurate than ours would be. The data from this test is recorded below.
Figure 4 Force Measurement Error Data comparing 30 seconds versus 6 seconds
Figure 5 % Force Measurement Error at each force point using different timing profiles
The results from the controlled test show additional error on all non-zero test points when comparing readings captured at 30 seconds against those captured at 6 seconds. It is important to note that the shear web-style load cell is one of the best types of load cells as far as creep characteristics.
What we are observing is some creep in the load cell. Per ASTM E74, creep is the change in deflection of the force measurement instrument under a constant applied force. And while some may say the error above is still acceptable, we must question if it really is. ISO 376 thinks the error warrants including a section about uniform loading that requires waiting at least 30 seconds. Plus, we compared the error at 6 seconds versus 30 seconds. What happens on the automated machines when the points are captured on the fly?
The results are clear to us, and the additional error is unacceptable. Morehouse has adopted best practices from ISO 376 and holds all calibration points for at least 30 seconds as recommended by ISO 376 and suggested by ASTM E74 when recording an ending zero.
Force Measurement Error - What does your calibration vendor do regarding timing between successive loadings?
If you enjoyed this article, check out our LinkedIn and YouTube channels for more helpful posts and videos.
We believe in changing how people think about force and torque calibration in everything we do. Morehouse believes in thinking differently about force and torque calibration and equipment. We challenge the "just calibrate it" mentality by educating our customers on what matters and what causes significant errors and focus on reducing them.
Morehouse makes our products simple to use and user-friendly. And we happen to make great force equipment and provide unparalleled calibration services.
Want to watch the video on why you should use Morehouse for your load cell calibration? It can be found here.
Please call 717-843-0081 to speak with a live person or email info@mhforce.com. You can also visit us on the web at mhforce.com.
# Time Interval Between Two Successive Loadings # Successive Loadings