Continuous Improvement in the Cal Lab
What if people could improve at a rate of 1 % per day? In approximately 70 days, they would be twice as effective at their job, and in 365 days, they would be 37.78343 times better.
In reality, 1 % better is not going to amount to much. For example, someone can decide to skip the burger and eat a salad on day one, but will that minor, fleeting change catapult a person into peak physical shape? No.
However, if someone continually chooses to eat a salad, take a walk, lift weights, and slowly shift their habits towards those who are in peak physical shape, what happens? They may become one of those people.
Many calibration companies need to look beyond processes, equipment, and accreditation, and begin focusing on employee engagement and a cycle of continuous improvement.
Think about these numbers in another way. If you were running a calibration laboratory with small incremental goals to become 1 % better per week, then the lab would be twice as good in seventy-two weeks.
Over time, these small habits could translate into being better at responding to customers, thus creating a more positive overall consumer experience. Or they could equate to studying a reservoir of technical content on calibration disciplines, thereby enhancing team members’ understanding of, and capabilities within, each discipline.
Imagine an employee who tries to be slightly more effective each day by learning more about their job and about ways to improve their performance. If the employee focused on becoming 1 % better for 225 working days, they would improve 1.01 ^225 or 9.382295 times compared to their effectiveness when they started. Any conscientious manager would dream of having that kind of progress in their company.
How about as a business? Can someone alter their habits just enough so that meaningful changes start to materialize? You can invest in people and the equipment necessary to do their job well. Additional training can be encouraged, and in some locations, there are even programs to help reimburse for training. Can companies abandon traditional concepts of cryptic goals and focus on improving the culture?
James Clear makes a poignant statement on the topic of goals. “You do not rise to the level of your goals. You fall to the level of your systems.” Simon Sinek adds to this idea by saying, “The goal is not to be perfect by the end. The goal is to be better today.”
Employee Engagement
Most laboratories rely on human beings to perform calibrations on designated equipment. As such, many companies are performing accredited calibration that relies on the technician’s judgment.
The process might be automated, but somewhere a person is often responsible for inspecting the equipment, hooking it up properly, running the test, and signing off on the results. People are responsible for checking the equipment and packaging it properly, as well as reviewing contracts and ensuring they can meet what their customers ask.
To foster effective workflow and positive outcomes, employees need to consistently make the right decisions in all facets of their job. When they are not engaged, not in the right role, or lack the appropriate leadership to support them, will the measurements they make have an increased probability of being incorrect?
We need to look to our most significant asset, our people, and focus on their engagement because engaged employees will be the ones that perpetuate a cycle of continuous improvement.
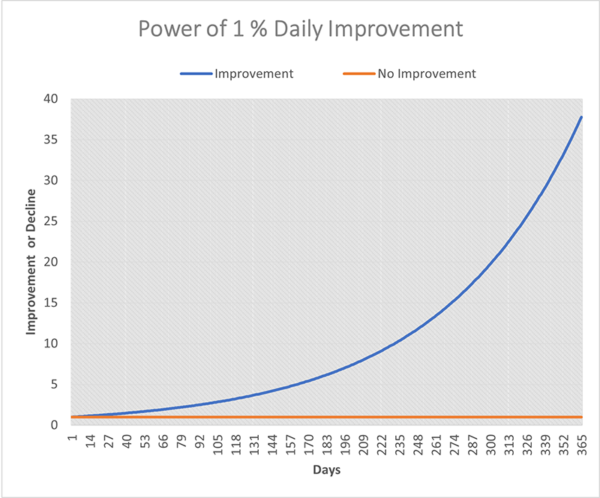
Employee engagement is an emotional state in which employees feel committed to their work. When these employees are in the metrology community, they continually refine their skills, keep up to date on the latest standards, become members of committees, and research new developments in their field.
An engaged employee does not accept procedural workarounds; instead, they strive to correct problematic issues. They certainly do not accept the maxim of “if it's not broken, don't fix it.” Essentially, engaged employees are highly motivated.
When companies focus their energy on establishing an effective culture, employees become empowered, and the organization, along with everyone in it, continually improves. Developing a culture of continuous improvement leads to better confidence in measurements made, ultimately creating a safer world.
Here at Morehouse, we are not perfect, though we continually strive to be better. Being better not only benefits us, but it also benefits our customers because when we are all engaged, measurement risk decreases. The outcome means more trust, which builds lasting partnerships.
Would you rather have a partner that works with you to help ensure you trust your measurements or a vendor that only provides a certificate? We are here to help if you choose to engage us.
If you enjoyed this article, check out our LinkedIn and YouTube channel for more helpful posts and videos.
#Continuous Improvement in the Cal Lab