A common question we get asked is, “If I have a tare weight, how do I correct it?” Thus, we are going to answer the question by discussing how to Correct for Tare Weight when using Load Cells or Proving Rings.
All instruments have different characteristics that may or may not require correction for the tare weight.
What is Tare Weight?
The tare weight is a “pre-load” on the reference standard. It is attributable to the weight of the moveable yoke, test instrument, bearing plate(s), load ball(s), and adapter fittings.
To answer this question, we will cover tare correction for the following instruments:
- Load Cells
- Proving Rings
Load Cell Tare Weight Correction
Load cells come in different shapes and sizes. Some load cells can withstand an overload of up to 150 % or more of rated capacity without damaging the load cell, and others only 110 %. When evaluating an additional error due to tare, one would need to compare the same force point with a tare load versus without.
In our lab, we have tested several load cells with variable results. We tested our shear web load cells by taring out up to 10 % of the rated capacity and then loading to 110 % versus loading the load cell to 100 %. That means on a 10,000 lbf load cell, we applied 1,000 lbf, hit tare on a meter, and then applied an additional 10,000 lbf, and compared the results against loading the load cell to 100 %.
We typically find that results will vary, depending on the type of load cell and the amount of tare load. The repeatability does not change much. However, the reproducibility does because we created a new variable by applying an additional 10 %, which introduces more stress onto the material. This creates more deflection, and the fractional change in length is measured by the strain gauges in the load cell.
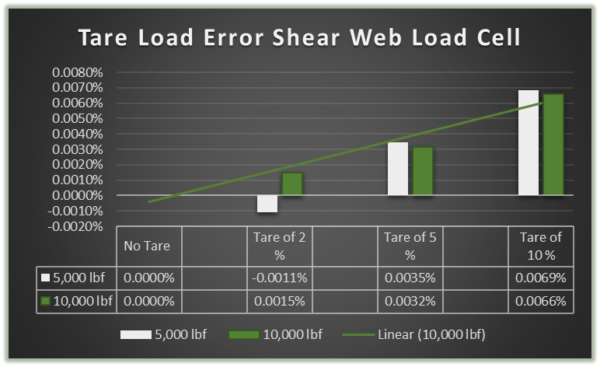
In cases where the “pre-load” is over 5 % of the capacity of the load cell, ignoring the tare load effect may introduce a significant error into the calibration. The error introduced can be determined by comparing two calculations.
First, calculate the load applied to the test instrument by treating the deflection of the calibration standard with the tare load applied as the “no-load” reading.
Next, calculate by taking into account the tare load. The tare load can be ascertained by weighing the items (yoke, test instrument, etc.) on a suitable platform scale. However, it may be more convenient to determine the tare load using a reference standard. The tare weight will have to be raised off of the load cell, and the Indicator should be zeroed. Then the weight can be lowered, and the weight can be calculated.
Comparing the results of these two calculations will readily show the error introduced. Once the weight is calculated, the user can test to determine an additional error.
How to Correct for Tare Weight when Using Load Cells Example: A 10,000 lbf load cell with a 200 lbf tare weight
The user zeros the load cell and applies the tare weight. The weight observed is 200 lbf. The indicator now reads 200 lbf. If one wants to apply 10,000 lbf, they need to apply 10,200 lbf, or they can hit tare and load to 10,000 lbf. The load cell will have a 10,200 lbf force applied regardless.
The best way to estimate the error is to first have the 10,000 lbf load cell calibrated to 10,200 lbf. Then compare the calculated deflection values at 10,200 lbf, deflection values at 200 lbf, and compare that against the calculated value at 10,000 lbf (see example below). Assuming the instrument fits the calibration curve well, the difference should be insignificant.

This example uses a Morehouse Ultra-Precision Load Cell. We have observed errors from 0.000 – 0.0025 % from various samples. Part of the issue in testing these low errors is that the repeatability and reproducibility errors of the load cell can be as high as ± 0.002 %. The resolution of the load itself could be 0.00050 % (50 % of the error at 5,000 lbf) and 0.00025 % (25 % of the error at 10,000 lbf).
Therefore, we consider this error insignificant because many claim their measurement uncertainty is between 0.02 % - 0.05 % of applied force.
How to Correct for Tare Weight when Using Load Cells Example: A 10,000 lbf load cell with a 500 lbf tare weight
The user zeros the load cell and applies the tare weight. The weight observed is 500 lbf. The indicator now reads 500 lbf. If one wants to apply 10,000 lbf, they need to apply 10,500 lbf, or they can hit tare and load to 10,000 lbf. The load cell will have a 10,500 lbf force applied regardless.
The best way to estimate the error is to first have the 10,000 lbf load cell calibrated to 10,500 lbf. Then compare the calculated deflection values at 10,500 lbf, deflection values at 500 lbf, and compare that against the calculated value at 10,000 lbf (see example below). Assuming the instrument fits the calibration curve well, the difference should be insignificant.

This example uses a Morehouse Ultra-Precision Load Cell. We have observed errors from 0.003 – 0.006 % from various samples. We consider this error significant because many claim their Measurement Uncertainty to be between 0.02 % - 0.05 % of applied force. To correct for the tare weight on a load cell steps might be taken to correct the error, or one might consider purchasing an additional load frame with less tare weight.
How to Correct for Tare Weight when Using Load Cells Example: A 10,000 lbf load cell with a 1,000 lbf tare weight (10 % of capacity)
The user zeros the load cell and applies the tare weight. The weight observed is 1,000 lbf. The indicator now reads 1,000 lbf. If one wants to apply 10,000 lbf, they need to apply 11,000 lbf, or they can hit tare and load to 10,000 lbf. The load cell will have an 11,000 lbf force applied to it.
The best way to estimate the error is to first have the 10,000 lbf load cell calibrated to 11,000 lbf. Then compare the calculated deflection values at 11,000 lbf, and deflection values at 1,000 lbf, and compare that against the calculated value at 10,000 lbf (see example below). Assuming the instrument fits the calibration curve well, the difference should be insignificant.

This example uses a Morehouse Ultra-Precision Load Cell. We have observed errors from 0.005 – 0.012 % from various samples. We consider this error significant because many claim their Measurement Uncertainty to be between 0.02 % - 0.1 % of applied force. To correct for the tare weight on a load cell steps should be taken to correct the error or purchase an additional load frame with less tare weight.
Tare Weight Correction for a Proving Ring
Unlike several load cells, proving rings do require a correction for tare. This is due to the inherent non-linearity of the rings. For analog proving rings, the position of the dial on the micrometer can be an additional error source. We have developed Excel sheets that help technicians use a proving ring with confidence and correct for tare properly.
Tare Load Correction Formula for a Proving Ring
Below is an example of a formula used to correct tare loads. The tare load correction formula corrects for tare and is applied to the value of the applied load from the fitted curve data provided with your calibration report.
The tare load correction formula is represented as follows: TCF = ((2 * A2) * L * T)) – A0
Where:
- A2 = The value of the A2 constant found on the ring calibration report
- L = The force value applied
- T = The force value of the tare applied
- A0 = The value of the constant found on the ring calibration report
Calibration Report Data:
- A2 = 0.2648421D-05
- L = 3,000.00
- T= 299.70 Lbf
- A0 = 0.1673432D+00
TCF = (2*0.2648421D-05*3000*299.70)-0.1673432D+00
TCF = 4.595 div
3,000 LBF = +1002.050 div. From table
1006.645 div. Correction for tare
Read the blog Proving Ring Tare Load Correction Proof for additional information on how to calculate the tare value.
How to Correct for Tare Weight when Using Load Cells - Conclusion
At Morehouse, we educate our customers and provide tools to explain How to Correct Tare Weight when using Load Cells or Proving Rings. Tare weight of less than 2 % is likely insignificant regarding the overall measurement uncertainty.
When the tare weight exceeds more than 2 % of the rated capacity of a load cell or proving ring, we urge for more testing to be done to capture error sources. If the tare weight is higher than 5 %, we recommend to calibrate the device to 105 to 110 % of the rated capacity to account for any of these errors. Correction formulas must be used for proving rings to obtain the correct deflection values.
I take great pride in our knowledgeable team at Morehouse, who continue to work with everyone, clarify complex topics, and provide tools to make you better. Tools like the Excel spreadsheet can be used to calculate expanded uncertainty at the time of calibration.
We have been in business for over a century and focus on being the most recognized name in the force business. That vision comes from educating our customers on what matters most, and having the proper discussions relating to force calibration concepts, so everyone uses the proper methods and math.
If you enjoyed this article, check out our LinkedIn and YouTube channel for more helpful posts and videos.
Everything we do, we believe in changing how people think about force and torque calibration. We challenge the "just calibrate it" mentality by educating our customers on what matters and what causes significant errors and focusing on reducing them.
In addition, Morehouse makes simple-to-use calibration products. We build excellent force equipment that is plumb, level, square, rigid and provide unparalleled calibration service with less than two-week lead times.
Contact us at 717-843-0081 to speak to a live person or email info@mhforce.com for more information.
#Load Cell Tare Weight
#Tare Weight
# How to Correct for Tare Weight when using Load Cells or Proving Rings
#Proving Ring Tare Weight