Force Measurement Terms
In the previous Back-to-Basics blog, I covered Load Cell Indicator Basics. This last blog for beginners contains a glossary of common terms in force measurement. This is a basic list of terms, and some have not been covered. It is important to post these for reference because most of these force measurement terms are used in speaking about the characteristics of load cells, measurement uncertainty, and calibration standards.
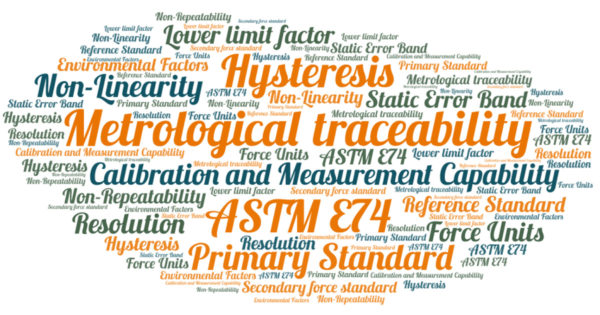
Force Measurement Terms
ASTM E74 – Standard Practices for Calibration and Verification for Force-Measuring Instruments: ASTM E74 is a practice that specifies procedures for the calibration of force-measuring instruments.
Best existing force-measuring instrument (ILAC P14): The term "best existing force-measuring instrument" is understood as a force-measuring instrument to be calibrated that is commercially or otherwise available for customers, even if it has a special performance (stability) or has a long history of calibration. For force calibrations, this is often a very stable force transducer (load cell) and indicator with enough resolution to observe differences in repeatability conditions.
Calibration and Measurement Capability (ILAC-P14): A CMC is a Calibration and Measurement Capability available to customers under normal conditions:
- as described in the laboratory's scope of accreditation granted by a signatory to the ILAC Arrangement; or
- as published in the BIPM key comparison database (KCDB) of the CIPM MRA.
The scope of accreditation of an accredited calibration laboratory shall include the Calibration and Measurement Capability (CMC) expressed in terms of:
- measurand or reference material;
- calibration/measurement method/procedure and/or type of instrument/material to be calibrated/measured;
- measurement range and additional parameters where applicable, e.g., frequency of applied voltage;
- uncertainty of measurement
Note: The scope of calibration is where one will find the best capability a company can achieve. It is important to check this when deciding on who to use for a calibration laboratory. If the scope says the best a company can do is 0.02 % from 1,000 lbf through 100,000 lbf, you cannot have uncertainty or accuracy better than that. Also, the best a company can do is usually what is reported on the certificate, though that does not mean that your equipment will be put in the same equipment as used for the CMC. It is imperative to ask the calibration provider about their measurement capability.
Morehouse can calibrate equipment up to 120,000 lbf known to within 0.0016 % of applied force. However, if someone sends in an instrument that is 36 inches long, we cannot fit it in that machine, and therefore, the best we can do is 0.01 % of applied in our elongated Universal Calibrating Machine.
Environmental Factors: Environmental conditions, such as temperature, influence the force transducer output. The most common specification is the temperature effect found on the force-measuring instrument's specification sheet. It is important to note that any deviation in environmental conditions from the temperature that the force-measuring instrument was calibrated at must be accounted for in the measurement uncertainty, using the user's force transducer measurements.
For example, the laboratory calibrated a force-measuring instrument at 23°C. The force-measuring instrument is then used from 13-33°C or ±10°C from the calibration. Based on the manufacturer's specification, this temperature variation could cause an additional change on the force output by 0.015 % reading per °C, or 0.15 % reading for ±10°C. This number is typically found on the force transducer's specification sheet as Temperature: Effect on Sensitivity, % Reading/100 °C or °F. The value will vary depending on the force transducer used. The example uses a common specification found for most shear-web-type force transducers.
Force Units: A force unit can be any unit representing a force. Common force units are N, kgf, lbf. The SI unit for force is N (Newton).
Hysteresis: The phenomenon in which the value of a physical property lags changes in the effect causing it, for instance when magnetic induction lags the magnetizing force. For force measurements, hysteresis is often defined as the algebraic difference between output at a given load descending from the maximum load and output at the same load ascending from the minimum load. Normally it is expressed in units of % full scale. It is normally calculated between 40 - 60 % of full scale.
Lower limit factor (LLF): This is an ASTM-specific term. The ASTM E74 standard uses a method of least squares to fit a polynomial function to the data points. The standard deviation of all the deviations from the predicted values by the fit function versus the observed values is found by taking the square root of the sum of all the squared deviations divided by the number of samples minus the degree of polynomial fit used minus one.
This number is then multiplied by a coverage factor (k) of 2.4 and then multiplied by the average ratio of force to deflection from the calibration data. The LLF is a statistical estimate of the error in forces computed from the calibration equation of a force-measuring instrument when the instrument is calibrated in accordance with this practice.
Metrological traceability (JCGM 200:2012, 2.41): Property of a measurement result whereby the result can be related to a reference through a documented unbroken chain of calibrations, each contributing to the measurement uncertainty.
Non-Linearity: The quality of a function that expresses a relationship that is not one of direct proportion. For force measurements, non-linearity is defined as the algebraic difference between the output at a specific load and the corresponding point on the straight line drawn between the outputs at minimum load and maximum load. Normally it is expressed in units of % of full scale. It is normally calculated between 40 - 60 % of full scale.
Non-Repeatability (per force transducer specification and not JCGM 200:2012): The maximum difference between output readings for repeated loadings under identical loading and environmental conditions. Normally expressed in units as a % of rated output (RO).
Other Force Measurement Errors: Most force-measuring instruments are susceptible to errors from misalignment, not exercising the force-measuring instrument to full capacity, and improper adapter use. There will be additional errors in almost all cases if the end user fails to have the force-measuring instrument calibrated with the same adapters being used in their application. Other errors may include temperature change under no-load conditions. Errors from loading equipment not being level, square and rigid can have significant contributions.
Primary Standard: Per ASTM E74, a deadweight force is applied directly without intervening mechanisms such as levers, hydraulic multipliers, or the like whose mass has been determined by comparison with reference standards traceable to the International System of Units (SI) of mass. NOTE: Weights used for force measurement require the correction for the effects of local gravity and air buoyancy and must be adjusted to within 0.005 % of nominal force value. The uncertainty budget for primary standards also needs to consider possible force-generating mechanisms other than gravity and air buoyancy, including magnetic, electrostatic, and aerodynamic effects.
Rated Output or RO: The output corresponding to capacity, equal to the algebraic difference between the signal at "(minimal load + capacity)" and the signal at minimum load.
Reference Standard(s) Calibration Uncertainty: This is usually the measurement uncertainty in the calibration of the reference standard(s) used to calibrate the force-measuring instrument.
Reference Standard(s) Stability: The change in the output of the reference standard(s) from one calibration to another. This number is found by comparing multiple calibrations against one another over time. If the instrument is new, the suggestion is to contact the manufacturer for stability estimation on similar instruments.
Repeatability condition of measurement, repeatability condition (JCGM 200:2012, 2.20): The condition of measurement, out of a set of conditions that includes the same measurement procedure, same operators, same measuring system, same operating conditions, and same location, and replicate measurements on the same or similar objects over a short period of time.
Measurement repeatability, Repeatability (JCGM 200:2012, VIM 2.21): Measurement precision under a set of repeatability conditions of measurement.
Repeatability can be calculated by taking the sample standard deviation of a series of at least two measurements at the same test point (three or more are recommended). The overall repeatability of more than one group of data is calculated by taking the square root of the average of variances, which is also known as pooled standard deviation. The purpose of this test is to determine the uncertainty of force generation in a force-calibrating machine or test frame. For laboratories testing multiple ranges, it is recommended that the measurement sequence takes a point for every 10% of the ranges they calibrate.
Example: A laboratory performing calibrations from 10 N through 10,000 N. The ranges calibrated may be 10 N - 100 N, 100 N - 1,000 N, and 1,000 N – 10,000 N. Recommended practice would be to take test points at 10, 20, 30, 40, 50, 60, 70, 80, 90, 100, 200, 300, 400, 500, 600, 700, 800, 900, 1,000, 2,000, 3,000, 4,000, 5,000, 6,000, 7,000, 8,000, 9,000, and 10,000 N.
For this application, zero should never be considered as a first test point. A force-measuring instrument should not be used to calibrate other force-measuring instruments outside the range it was calibrated over. A force-measuring instrument calibrated from 10 % through 100 % of its range may not be capable of calibrating force-measuring instruments outside of this range.
Resolution (JCGM 200:2012, VIM 4.14): The smallest change in a quantity being measured that causes a perceptible change in the corresponding indication.
Resolution of a Displaying Device (JCGM 200:2012, VIM 4.15): The smallest difference between displayed indications that can be meaningfully distinguished.
Reproducibility condition of measurement, reproducibility condition (JCGM 200:2012, VIM 2.24): The condition of measurement out of a set of conditions that includes different locations, operators, measuring systems, and replicate measurements on the same or similar objects.
Measurement reproducibility, Reproducibility (JCGM 200:2012, VIM 2.25): Measurement precision under reproducibility conditions of measurement.
Reproducibility calculations between technicians can be found by taking the standard deviation of the averages of the same test point taken multiple times (multiple groups). There are other acceptable methods for determining reproducibility, and it is up to the end user to evaluate their process and determine if the method presented makes sense for them. For guidance on Repeatability and Reproducibility, the user should consult ISO 5725 Parts 1 - 6.
Secondary force standard (ASTM E74): An instrument or mechanism, the calibration of which has been established by comparison with primary force standards.
Static Error Band: The band of maximum deviations of the ascending and descending calibration points from a best-fit line through zero output. It includes the effects of non-linearity, hysteresis, and non-return to minimum load. It is normally expressed in units of %FS.
Back-to-Basics series:
- Force Calibration and its Importance
- How a Transducer Measures Force
- Compression and Tension Force Calibration
- Calibration versus Verification
- Measurement Uncertainty
- Load Cell Terminology
- Types of Load Cells
- Load Cell Troubleshooting
- Load Cell Indicator Basics
- Force Measurement Glossary of Terms
Force Measurement Terms - Conclusion
I take great pride in our knowledgeable team at Morehouse, who will work with you to find the right solution. We have been in business for over a century and focus on being the most recognized name in the force business. That vision comes from educating our customers on what matters most, and having the right discussions relating to force measurement so that everyone speaks the same language in relation to force measurement terms.
If you enjoyed this article, check out our LinkedIn and YouTube channel for more helpful posts and videos.
Everything we do, we believe in changing how people think about force measurement and torque calibration. We challenge the "just calibrate it" mentality by educating our customers on what matters, and what causes significant errors, and focus on reducing them.
Morehouse makes simple-to-use calibration products. We build excellent force equipment that is plumb, level, square, and rigid and provide unparalleled calibration service with less than two-week lead times.
Want to watch the video on why use Morehouse for your load cell calibration? That can be found here.
Please contact us @ 717-843-0081 to talk to a live person or email info@mhforce.com. Visit us on the web at mhforce.com.
Force Measurement Terms References
VIM: International vocabulary of metrology
#Force Measurement Terms
#Force Measurement