Guide for Understanding Uncertainties on a Morehouse ASTM E74 Calibration Certificate
Reporting the Expanded Uncertainty on an ASTM E74 Calibration Certificate of the measurement is a requirement of ISO/IEC 17025 and likely always will be. However, if you look at several different certificates of calibration, their Expanded Uncertainty reported, contributors and reporting methods will vary greatly. Some include a blanket statement of uncertainty, while others simply ignore significant contributions required by several published standards. This guide describes the formulas, statements, and data reported on a Morehouse ASTM E74 calibration certificate and how it benefits the end users.
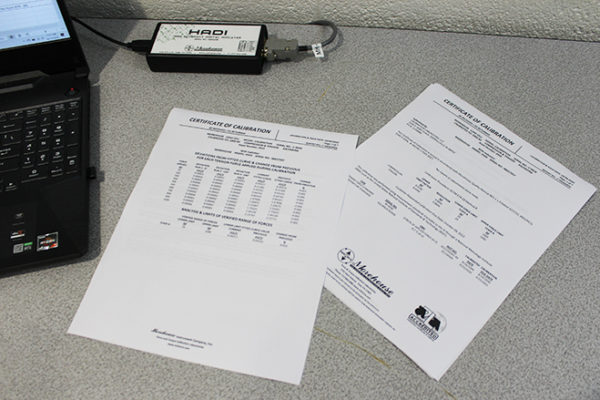
At Morehouse, we follow the proper requirements per our accreditation and rely heavily on meeting the requirements of ISO/IEC 17025:2017 and these published documents:
- ILAC-P14 "Policy for Measurement Uncertainty in Calibration" (1)
- JCGM 100:2008 "Evaluation of measurement data — Guide to the expression of uncertainty in measurement" (2)
- ANSI/NCSL Z540.3 & Handbook "Requirements for the Calibration of Measuring and Test Equipment" (3)
Morehouse also follows general acceptable metrological practices, such as the NIST technical Note 1297, "Guidelines for Evaluating and Expressing the Uncertainty of NIST Measurement Results." (5) The Appendix on a Morehouse ASTM E74 calibration certificate uses a similar method to what is found on a calibration report from NIST. The difference is that Morehouse includes the resolution of the Unit Under Test (UUT) because it is required by ILAC-P14. Therefore, Morehouse follows the ILAC-P14 requirements by reporting Expanded Uncertainty per point and replicates NIST's method in the appendix with one modification to include the resolution of the UUT (see Figure 1).
Figure 1: Last Page of the NIST ASTM E74 Calibration Certificate for Morehouse 4.45 MN Reference Standard
NIST Formula for Measurement Uncertainty from Figure 1 is uc² = ur² + uw² + uv²
Morehouse Formula for Measurement Uncertainty, which needs to follow ILAC-P14 is uc² = ur² + uw² + ures² + uv²
Requirements for Reporting Measurement Uncertainty on an ASTM E74 Calibration Certificate
The two formulas above are very similar and follow the approach found in JCGM 100:2008 (2), except the Morehouse formula also includes the resolution of the UUT (ures2). The reason for the difference is that Morehouse must adhere to ILAC-P14 Section 5.4, which states, "Contributions to the uncertainty stated on the calibration certificate shall include relevant short-term contributions during calibration and contributions that can reasonably be attributed to the customer's device. Where applicable, the uncertainty shall cover the same contributions to the uncertainty that were included in the evaluation of the CMC uncertainty component, except that uncertainty components evaluated for the best existing device shall be replaced with those of the customer's device."(1)
For short-term contributions, it is generally accepted that the repeatability and resolution of the Unit Under Test (UUT) should be included unless the repeatability is dominant. Otherwise including the resolution may not be required. ILAC-P14 Section 4.3, Note 2 states, "When it is possible that the best existing device can have a contribution to the uncertainty from repeatability equal to zero, this value may be used in the evaluation of the CMC. However, other fixed uncertainties associated with the best existing device shall be included." (1) Therefore, in most cases when a load cell or other instrument is not moved, and the force machine is plumb, level, square, and rigid enough to not yield deviation in the same position, then we opt to include the resolution of the UUT in the reported expanded uncertainty.
The ANSI/NCSL Z540.3 handbook further supports these contributors by stating, "The value of this uncertainty estimate should reflect the results that are reasonably expected from the use of the approved procedure to calibrate the particular Type of M&TE. Therefore, the estimate includes all components of error that influence the measurement results of the calibration, which would also include the influences of the item being calibrated with the exception of the bias of the M&TE. Therefore, the calibration process error includes temporary and non-correctable influences incurred during the calibration such as repeatability, resolution, error in the measurement source, operator error, error in correction factors, environmental influences, etc." (3)
The end-user must do additional repeatability studies and account for other error sources per JCGM 100:2008 (2) and back out the contributors to uncertainty; we list the short-term contributors as required by ILAC-P14 in Morehouse certificates. The expanded uncertainty will be the absolute best the instrument can perform in our laboratory. These contributors follow ILAC-P10 "Policy on the Metrological Traceability of Measurement Results" (4). The end-user should break down all of the uncertainty contributors, calculate the appropriate coverage factor using the effective degrees of freedom, or correct Type-A data at the source using the student's t correction, which turns most Type-A data into data with unlimited degrees of freedom. The importance of correcting Type A data would be if someone wanted to use a coverage factor of k = 2. The Welch-Satterthwaite equation may yield varying k values when used to correspond to a confidence interval of 95 %. Both methods are outlined in the Morehouse CMC-CALCULATIONS-FOR-FORCE-MEASUREMENTS Microsoft Excel spreadsheet.
The contributions for the CMC uncertainty parameter for an ASTM E74 calibration are as follows:
Type A Uncertainty Contributions
- ASTM LLF reported as 1 Standard Deviation (k=1). ASTM LLF is reported with k= 2.4.
Note: The reason ASTM LLF is called out is that many reports do not list the standard deviation. In actuality, the Standard Deviation per section 8 of the ASTM E74 standard is what is required. - Repeatability conducted with the Best Existing Force measuring instrument
- Repeatability and Reproducibility
Note: Repeatability and Reproducibility are from an R & R study and should not be confused with repeatability with the Best Existing Force measuring instrument, as noted in 2 above. It is up to the end-user to determine if these errors are significant and included in the final uncertainty budget.
Type B Uncertainty Contributors
- Resolution of the Best Existing Force measuring instrument
- Reference Standard Resolution (if applicable)
- Reference Standard Uncertainty
- Reference Standard Stability
- Environmental Factors
- Other Error Sources
Note: All uncertainty contributions should be combined. If appropriate, the Welch-Satterthwaite equation described in JCGM 100:2008 should be used to determine the effective degrees of freedom for the appropriate coverage factor for a 95 % confidence interval.
For more information on what is needed for proper force measurement uncertainty budgets, there is a detailed guidance document published by A2LA G126 - Guidance on Uncertainty Budgets for Force Measuring Devices. The 21-page document further explains definitions, terms, and requirements to complete a full uncertainty budget. Morehouse has an uncertainty template in Microsoft Excel to help any calibration laboratory that needs to meet the ISO/IEC 17025 requirements and set up its budget. The file can be downloaded at measurementuncertainty.info
Morehouse Measurement Expanded Uncertainty Calculations on the primary Certificate of Calibration
On our Certificate of Calibration for ASTM E74 calibrations, Morehouse states the following "The Expanded Uncertainty is the aggregate uncertainty of the Morehouse measurement process, which includes the uncertainty of the reference standards used for calibration and the resolution. It is stated with a coverage factor of k=2, such that the confidence interval corresponds to approximately 95 %."
When Morehouse reports the Expanded Uncertainty, we use the formula uc² = uw² + ures² + uv² for the combined standard uncertainty where
uw is the maximum standard Uncertainty for the Calibration and Measurement Capability (CMC) of the force devices used for calibration.
For deadweights, uw represents the estimated standard deviation in the forces applied by the deadweight standards due to the uncertainties in the determination of the mass, air density, and gravitational acceleration and includes contributions from the measurement process such as repeatability studies, the resolution of the best existing device, and environmental factors. For transfer standards, the CMC includes the uncertainties from NIST calibrations, reference standard uncertainty, repeatability studies, stability of the reference standard, resolution of the reference, and the best existing device, environmental factors, and other error sources associated with the Morehouse calibrating machines and measurement process
ures is the resolution of the force measuring system at the time of calibration.
uv is the standard uncertainty in the calibration of the voltage-ratio measurement instrumentation used at Morehouse. This term is 0 for an indicator that is supplied with the transducer to be calibrated together as a system.
Figure 2: Page from Morehouse ASTM E74 Certificate
The combined standard uncertainty is then multiplied by the appropriate coverage factor, typically k = 2, and the Expanded Uncertainty is reported.
Figure 3: Uncertainty Calculation for ASTM E74 Calibration Certificate
Formulas for Measurement Uncertainty on ASTM E74 Calibration Certificate Reports in the appendix.
Morehouse Formula for Measurement Uncertainty uc² = ur² + uw² + ures² + uv²
NIST Formula for Measurement Uncertainty uc² = ur² + uw² + uv²
When we follow what NIST does in our appendix, we add in ures to the equation, where ures is the resolution of the force measuring system at the time of calibration.
Figure 4: Page from the Morehouse certificate appendix
The formula uc² = ur² + uw² + ures² + uv² is simple to follow. However, we will break it down further so you can check it using Microsoft Excel.
Standard uncertainty for this example
Figure 5: Uncertainty calculation to support the Morehouse Appendix
- We break down the individual components and reduce them to k =1
- uw is found by either taking the percentage force of the CMC uncertainty for the reference force machines times the force applied a fixed value or a formula for the reference standard uncertainty. In this example, Morehouse used deadweights known to be within 0.0016 %, so we multiplied the force applied by this number.
- uv is found by multiplying the percentage of the CMC uncertainty for the reference indicator by the force applied.
- ur is the ASTM LLF from the calibration report. This is found by dividing the LLF by a coverage factor of k = 2.4 since that is what ASTM E74 uses for the LLF.
- ures is the resolution of the force measuring device divided by the appropriate divisor. In this example, it is the square root of 12 or 3.464.
- All of these numbers can be found in Microsoft Excel by using this formula SQRT((uw^2)+(uv^2)+(ur^2)+(ures^2))
- Then Expanded Uncertainty is found by multiplying by the coverage factor. In this case, it is 2.
Figure 6: As a % and Response Units
- To find the percentage, divide the uncertainty by the force applied and multiply by 100.
- To find Response units, multiply the percentage by the unit's output under test at that force point.
If you enjoyed this article, check out our LinkedIn and YouTube channels for more helpful posts and videos.
I take great pride in our knowledgeable team at Morehouse, who will work with you to find the right solution. We have been in business for over a century and have a focus on being the most recognized name in the force business. That vision comes from educating our customers on what matters most and having the right discussions relating to calculating measurement uncertainty per the right documents to meet the ISO/IEC 17025: 2017 guidelines.
We believe in changing how people think about force and torque calibration in everything we do. We challenge the "just calibrate it" mentality by educating our customers on what matters and what causes significant errors, and focus on reducing them.
Morehouse makes simple-to-use calibration products. We build awesome force equipment that is plumb, level, square, and rigid, and we provide unparalleled calibration service with less than two weeks' lead times.
Contact us at 717-843-0081 to speak to a live person or email info@mhforce.com for more information.