Unbolting Load Cells May Not Produce Repeatable Calibration Results
Unbolting Load Cells might be common practice, though the errors associated with this practice can be quite high. This article discusses ways to minimize these errors regarding unbolting load cells.
Bolting a Load Cell Thread Class and Torque Applied
• Morehouse recommends bolting a load cell to a base before sending it to us for calibration.
• Error sources from a different class of threads and different bolting procedures can be quite large.
• If the load cell must be bolted to a base, the bolts used to attach it to a base should be sent in, and a base of similar material and flatness to what it is being used with should be sent in.
• Variability between technicians, bolts, the flatness of the base, etc., will increase measurement error and may be difficult to quantify.
If you are working to a standard such as ASTM E74 or another ASTM standard that references ASTM E4, you must have your equipment calibrated according to the ASTM E74 procedure. The ASTM E4 Annex allows the force-measuring devices to be removed from the testing machine under various circumstances. ANNEX A1. VERIFYING THE FORCE MEASURING SYSTEM OUT OF THE TEST MACHINE in the ASTM E4 procedure lists the reasons to perform a force measuring system verification out of the test machine. These reasons include: Inadequate spacing within the testing application load train to allow placement of the force standard, physically impossible to apply a primary dead-weight force in the compression mode without removal of the force measuring system (note: The force measuring system includes the indicator) and test rigs that do not have a reaction frame.
However, if removing the force-measuring device from the machine requires unbolting load cells, there could be large measurement errors such as not bolting to the right torque specification, having different operators using different methods, not bolting in a star pattern, and other errors discussed below.
Not bolting to the right torque specification.
Pictured below, we have an ASTM E74 calibration on a 60,000 lbf load cell bolted to 25 lbf-ft. This is the specification for a compression load cell. All of the bolts were tightened to this specification. When comparing these numbers against the same load cell bolted to 45 lbf-ft, the output is different. When bolted properly, the change in output is about 0.7 % different, and the deviations between the observed values and the fitted curve are much less. The cell's performance is 100 % better in tension when bolted properly.
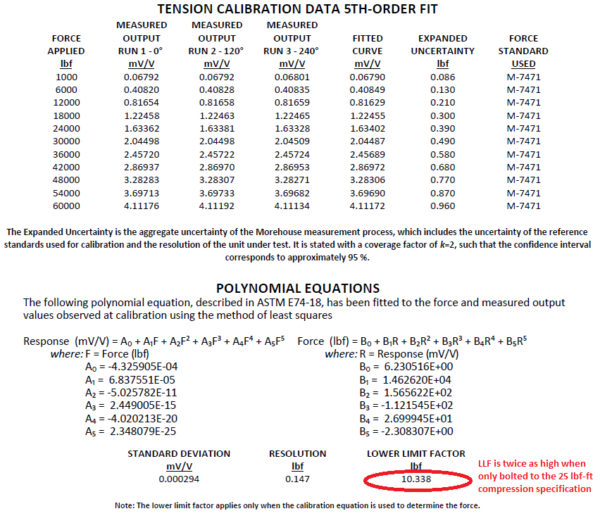
Load Cell Bolted to 25 lbf-ft.
Picture of Bolting Patterns for Load Cells
The end-user should always perform the bolting as different operators, and methods have hard to quantify errors
Unbolting Load Cells is not a good practice!
The equipment's end-user should bolt down any cell that needs to be calibrated before being sent anywhere for calibration. When you send a load cell that requires bolting, you should not expect the calibration results to be valid for your testing needs. If you are not testing the load cell in the machine, it is being used in; you will need to account for additional errors due to the following; mounting considerations, variation between different bolts, material in the base, surface finish on the base, hardness, stiffness, alignment, flatness, bending, and variations from using different bolting sequences may contribute to the uncertainty. Lets us not forget the torque wrench that may be accurate to 4 % of applied torque used to torque the bolts. This assumes a torque wrench was even used.
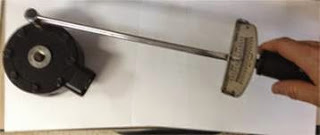
I hope by now, most of you are starting to understand that this type of calibration has several major possible uncertainty contributors that all need to be addressed. Even if all of these potential errors are quantified, my bet is an R & R study has not been performed between the technicians installing the load cell in the machine and the technicians in the laboratory performing the calibration.
Is there a significant difference between these technicians? I'm going to go on record and say " You Betcha" unless a very rigid testing procedure was documented, and you have SPC charts to prove it. I assume that any lab going to these great lengths to quantify all of these errors has already realized that there is probably a better way to ensure more repeatable results.
Morehouse will always suggest purchasing the proper equipment that will allow for calibration of the load cells in the machines they are being used. Two excellent standards will give you detailed instructions on using a load cell system to calibrate these load cells in place. These standards are ASTM E4 and ISO 7500. Morehouse can provide a complete load cell system with ISO/IEC 17025 accredited calibration in accordance with ASTM E74 or ISO 376 to perform in-place calibrations of load cells in the machines, they are being used.
If you are working to ASTM standards that reference ASTM E4 as a calibration requirement, it is important to note that the entire system needs to be calibrated if removed. When equipment is not available to allow for in-place calibrations, please remember to account for the various uncertainty contributors listed above in addition to environmental conditions, the uncertainty of the reference standards used to perform the calibration, the resolution of the device, the stability of the instrumentation and the reproducibility and repeatability of the measurement process.
Also, please remember that Unbolting Load Cells from the base voids the warranty for most load cell manufacturers.
Unbolting Load Cells May not Produce Repeatable Calibration Results - Conclusion
Unbolting load cells is generally a bad idea for these force-measuring devices. Accounting for all of the additional error sources and measurement traceability can be problematic. If you are in a situation where unbolting load cells is required, please feel free to contact the Morehouse support team to ensure you are following the best-recommended calibration guidelines in hopes of limiting the overall measurement error and risk.
If you enjoyed this article, check out our LinkedIn and YouTube channel for more helpful posts and videos.
I take great pride in our knowledgeable team at Morehouse, who will work with you to find the right solution. We have now been in business for over a century and focus on being the most recognized name in the force business. That vision comes from educating our customers on what matters most and having the right discussions. Morehouse will not commit to providing a system if we cannot meet your expectations.
Everything we do, we believe in changing how people think about force and torque calibration. We challenge the "just calibrate it" mentality by educating our customers on what matters, and what causes significant errors, and focusing on reducing them.
Morehouse makes simple-to-use calibration products. We build awesome force equipment that is plumb, level, square, rigid, and provide unparalleled calibration service with less than two-week lead times.
Contact us at 717-843-0081 to speak to a live person or email info@mhforce.com for more information.
Note: This blog on Unbolting Load Cells was updated on 11/11/2020 with additional content.
#Unbolting Load Cells