Load Cell Specifications Explained
Figure 1 Example of a Typical Morehouse Load Cell Specifications Sheet
Load cells are precision devices used to measure force or weight, and their performance is defined by various specifications.
The purpose of this article is to explain the typical load cell specifications sheet.
Let's break down the key parameters from a typical Morehouse Load Cell Specifications Sheet and explain what each of them means:
Accuracy Parameters:
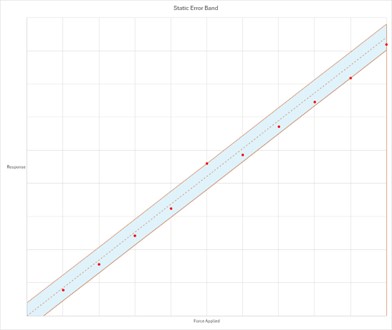
Static Error Band (SEB), % R.O.: This represents a subset of errors in the load cell’s output, including sources such as non-linearity, hysteresis, and return to zero after loading. A lower SEB means higher accuracy. For example, the static error band for smaller capacities is ±0.02 % R.O., meaning the error is within 0.02 % of the rated output (R.O.).
Our goal is to find a line that results in the smallest, maximum error. This line also needs to fit through the origin (0, 0), so only the slope needs to be calculated via (y1+y2) / (x1+x2). The best approach to this is to iterate across every pair of percent force applied of full scale (% FS) and the zero adjusted responses.
For each pair, calculate the slope, use the slope to calculate the percent error for all % FS, and take the largest error as that slope's "absolute error" value. Repeat this for all possibilities, taking the slope that has the smallest absolute error value.
Figure 3 Load Cell Specifications Non-Linearity Example
Non-Linearity, % R.O.(Rated Output): This specifies the deviation from a straight line when force is applied. A lower value indicates that the load cell response is more linear, which is ideal for precise measurements. Reported Non-linearity can vary for the same cell depending on how this straight line is defined. Typical definitions are endpoint, best fit straight line, and best fit straight line through zero. The SEB example above uses the best fit straight line thru zero to calculate the linearity.
An ideal measurement device has a perfectly linear response to force applied ratio. However, this is rarely true; most devices have a non-linear ratio. The purpose of the non-linearity calculation is to show how the recorded responses deviate from the ideal ratio. Non-linearity is typically expressed in the percent of full-scale (% FS).
Figure 4 Load Cell Specifications Hysteresis Example
Hysteresis, % R.O.: Hysteresis measures the difference in output between ascending and descending values. It reflects the load cell’s ability to return to its initial state. Lower hysteresis values (as low as ±0.02 %) indicate less error and better accuracy.
For force measurements, Hysteresis is defined as the difference between two responses of a single given load, one ascending from the lowest non-zero load applied, and the other descending from the full-scale load. Hysteresis is typically calculated near 50% load.
Figure 5 Load Cell Specifications Non-Repeatability Example
Non-Repeatability, % R.O.: This is the maximum difference between repeated measurements under the same conditions. Non-repeatability values as low as ±0.005 % show that the load cells produce very consistent results.
Non-repeatability = ABS(Run1-Run2)/AVERAGE (Run1, Run2, Run3) *100
Non-repeatability tells the user a lot about the performance of the load cell. It is important to note that non-repeatability does not tell the user about the load cell's reproducibility or how it will perform under different loading conditions (randomizing the loading conditions). At Morehouse, we have observed numerous load cells with good non-repeatability specifications that do not perform well when the loading conditions are randomized, or the load cell is rotated 120 degrees as required by ISO 376 and ASTM E74.
Figure 6 Load Cell Specifications Creep Example
- Creep, % Rdg(Reading)/20 Min: Creep measures how much the load cell's output drifts when a constant load is applied over time. Low creep values (±0.01 %) indicate that the output remains stable, even during long measurements. More information on load cell creep can be found here.
- Off-Center Load Sensitivity (%/in): This specification refers to how much the load cell’s output changes when a load is applied off-center, i.e., not directly along the central axis of the load cell.
If a load is not perfectly centered on the load cell, it can create bending or uneven force distribution. The off-center load sensitivity quantifies how sensitive the load cell is to this type of misalignment.
Example from the Load Cell Specification: In the datasheet, off-center load sensitivity is specified as ±0.1 %/in. This means that if the load is applied 1 inch away from the center of the load cell, the output could deviate by up to 0.1 % of the rated output.
- Side Load Sensitivity (%): Side load sensitivity measures how much the load cell’s output changes when a force is applied perpendicularly or laterally, rather than along the intended load axis.
Side loads can introduce measurement errors by causing strain on parts of the load cell that are not designed to measure force in those directions. High side load sensitivity would make the load cell less accurate under such conditions.
Example from the Load Cell Specification: The side load sensitivity in the datasheet is also listed as ±0.1 %. This means that if a side load is applied, the output could deviate by 0.1 % of the rated output. This specification indicates the load cell’s ability to minimize errors when forces are applied in directions other than the primary loading axis.
- Zero Balance (% R.O.): Zero balance refers to the output signal of the load cell when no load is applied. Ideally, the output should be zero when no force is acting on the load cell. However, due to manufacturing tolerances, material properties, and slight imbalances in the strain gauges, there is usually a small non-zero output even when the load is at zero. This small output is referred to as the zero balance.
Zero balance is typically expressed as a percentage of the Rated Output (R.O.). In the specification sheet for the Ultra Precision Shear Web Load Cells, the zero balance is listed as ±1.0% R.O. This means that when there is no load on the load cell, the output could be up to 1% of the rated output in either direction (positive or negative).
2. Temperature Specifications:
- Temperature Range, Compensated (°F): The compensated temperature range (+15°F to +115°F) is the range within which the load cell compensates for temperature effects to maintain accuracy. Outside of this range, temperature fluctuations might affect the accuracy of measurements.
- Temperature Range, Operating (°F): The operating range (-65°F to +200°F) is broader than the compensated range. The load cell can function within this range but may experience more temperature-related errors outside the compensated range.
- Sensitivity Effect, % Rdg / 100°F: This represents how much the load cell's sensitivity changes with temperature. The specification indicates that the sensitivity may change by 0.08 % of the reading for every 100° F temperature change.
- Zero Effect, % R.O. / 100°F: This parameter measures the change in zero balance (the output when no load is applied) due to temperature variations. Like the sensitivity effect, the zero effect is minimal, with a change of 0.08 % R.O. per 100° F.
3. Electrical Specifications:
- Input/Output Resistance (Ω): These parameters describe the electrical characteristics of the load cell. These values ensure the electrical compatibility of the load cell with measurement systems. More information on Input/Output resistance can be found here.
- Sensitivity: Sensitivity is also referred to as Rated Output (R.O.) or Full-Scale Output (F.S.O or F.S.). Sensitivity defines the nominal output signal produced by the load cell for each volt of excitation voltage applied. For example, for a 10,000 lbf capacity load cell, the sensitivity is 4 mV/V, meaning the output voltage would be 4 millivolts per volt of excitation.
- Insulation Resistance (MegΩ @ 50 VDC): This parameter indicates how well the load cell's electrical circuits are isolated from its body, reducing the chances of electrical interference. With an insulation resistance of 5000 Megohms, the load cell is well-protected against electrical noise.
4. Mechanical Specifications:
- Safe Overload, % R.O.: This is the amount of overload a load cell can withstand without being damaged. In our example, the Morehouse load cell can handle overloads up to 150 % of its rated output without permanent damage.
- Weight and Material: The load cells are available in various capacities, ranging from grams to millions of lbf. Depending on the capacity, the load cells are made from aluminum or steel, affecting their weight and suitability for different applications. In our example, a 300 lbf load cell weighs around 3.8 lb., while a 200,000 lbf load cell weighs 171 lb.
Figure 7 Multiple Morehouse Load Cells
Note: Morehouse has several load cells, many with slightly different load cell specifications.
All Morehouse load cells are designed with temperature compensation to minimize errors caused by temperature fluctuations.
This compensation ensures accurate measurements even in varying temperature environments.
Temperature compensation helps correct the sensitivity and zero-balance shifts mentioned earlier, ensuring that performance remains consistent across the compensated temperature range.
Figure 8 Morehouse Datasheet Example Showing ASTM E74 and ISO 376 Performance
Load Cell Specifications Explained Conclusion:
Each load cell specification on the load cell datasheet is crucial for understanding the performance, accuracy, and environmental limits of the device.
The electrical, mechanical, and thermal characteristics work together to provide highly accurate and reliable force measurements across a wide range of conditions.
One key detail Morehouse will provide is how well the load cell will perform regarding ASTM E74 requirements as well as ISO 376 on our datasheet.
These numbers often tell one about the expected performance of the load cell when used under similar conditions at which it was calibrated.
For further details on calculations related to these load cell specifications, you can refer to Morehouse’s calculation guidance (Morehouse-Calculation-Guidance), which covers advanced topics such as non-linearity, hysteresis, and other force measurement-related factors, and the calculations used to determine many specifications.
More Information about Morehouse
We believe in changing how people think about force and torque calibration in everything we do.
This includes setting expectations and challenging the "just calibrate it" mentality by educating our customers on what matters and what may cause significant errors.
We focus on reducing these errors and making our products simple and user-friendly.
This means your instruments will pass calibration more often and produce more precise measurements, giving you the confidence to focus on your business.
Companies around the globe rely on Morehouse for accuracy and speed.
Our measurement uncertainties are 10-50 times lower than the competition, providing you more accuracy and precision in force measurement.
We turn around your equipment in 7-10 business days so you can return to work quickly and save money.
When you choose Morehouse, you're not just paying for a calibration service or a load cell.
You're investing in peace of mind, knowing your equipment is calibrated accurately and on time.
Contact Morehouse at info@mhforce.com to learn more about our calibration services and load cell products.
Email us if you ever want to chat or have questions about a blog.
We love talking about this stuff. We have many more topics other than expressing SI units!
Our YouTube channel has videos on various force and torque calibration topics here.
# load cell specifications