Does a Backup Load Cell Meter for Your Load Cell System Make Sense?
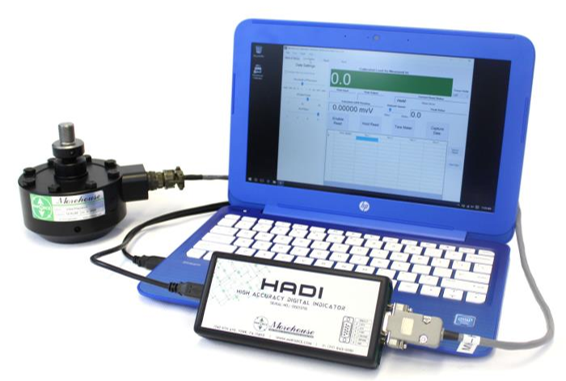
Backup Load Cell Meter - Reason Why On Might be Needed
A client has four load cells on one meter, and the technician loses, drops, or breaks the current indicator. This is a scenario we see happen quite a bit. If Murphy can strike, chances are it will eventually occur. We have had numerous clients ask us about how to back up or how to substitute a meter after the inevitable happens.
The main problem is it may be too late at this point as the system was calibrated with the now damaged meter. If you are reading this thinking about things, the chances are that you have been in this situation. Thus, it might now be time to consider a backup load cell meter.
Knowing you have to pay to have your system calibrated again is not a great feeling; now you've lost all of the calibration histories with that meter. This is why we often recommend pairing one load cell with one meter as that is the absolute best practice without further complicating the measurement traceability chain. The second best option would be to have a backup meter. This involves standardizing to a traceable measurement.
It is almost always accomplished by using a load cell simulator to generate mV/V. It is also compliant with ASTM E74 found in section 12, which states, " It may be desirable to treat the calibration of the elastic member and the force-indicating instrument separately, thus allowing for the substitution or repair of the force-indicating instrument without the necessity for repeating an end-to-end system calibration. When such substitution or repair is made, the user assumes the responsibility to ensure that the accuracy of the force-measuring system is maintained.?
To do a substitution on a backup load cell meter, the following must occur:
- The electronic-indicating instrument used in the initial calibration and the instrument to be substituted shall each have been calibrated and their measurement uncertainties determined.
- The electronic indicating instrument to be substituted shall be calibrated with traceability to the SI over the full range of its intended use including both positive and negative values if the system is used in tension and compression.
- The calibrated range shall include a point less than or equal to the output of the force transducer at the lower force limit and a point equal to or greater than the output of the force transducer at the maximum applied force.
- A minimum of five points shall be taken within this range.
- The measurement uncertainty of each electronic indicating instrument shall be less than or equal to one-third of the uncertainty for the force-measuring system over the range from the lower force limit to the maximum force. (0.000033 mV/V for Class AA and 0.000165 mV/V for Class A) Note: The Morehouse HADI is more than capable of this!
- The measurement uncertainty of the force-indicating instrument shall be determined by one of the methods outlined in Appendix X2.
- It is recommended that a transducer simulator capable of providing a series of input mV/V steps over the range of measurement and with impedance characteristics similar to that of the force transducer be employed as a check standard to verify the calibration of the electronic indicating instrument and in establishing the measurement uncertainty
- The measurement uncertainty of the transducer simulator shall be less than or equal to one-tenth of the uncertainty for the force-measuring instrument.
- Excitation voltage amplitude, frequency, and waveform shall be maintained in the substitution within limits to ensure that the effect on the calibration is negligible
- It is a user's responsibility to determine limits on these parameters through measurement uncertainty analysis and appropriate tests to ensure that this requirement is met.
- The substitution of an interconnect cable can have a significant effect on calibration. If an interconnect cable is to be substituted
To demonstrate this, we have a table below using a load cell simulator to simulate one direction of calibration using two Morehouse HADI Meters.
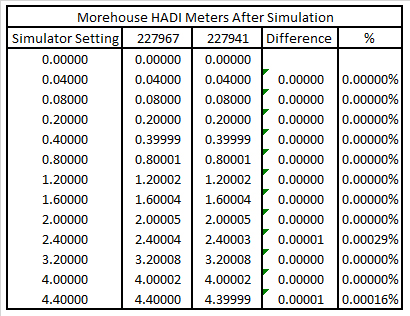
The simulator was calibrated by a Fluke 8508 using the ratiometric measurement traceable through calibration at Fluke. The actual transfer of the simulator and uncertainty was better than 0.001 %. (Note: This must be included in the calculation of measurement uncertainty). Additional contributors such as Resolution (not mentioned in ASTM E74, but should be included), Indicator Non-Linearity, Temperature effect on the gain, and other error sources. Per Annex X4, "The allowable uncertainty for this electronic indicating instrument calibrated for use over the Class AA verified range of forces is 0.05 % of 0.2 mV/V expressed in electrical units or 0.0001 mV/V.
Allowable uncertainty for the force-indicating instrument is one-third of this limit or 0.000033 mV/V. If the uncertainty is less than 0.000033 mV/V, as in this example, the substitution is permitted." For Class A verified range of forces, the number becomes five times greater or 0.000165 mV/V to maintain one-third of the limit and allow substitution. In the example above, we are demonstrating phenomenal results comparing two different Morehouse HAD indicators. Only 2 of the 12 points show any difference, and that difference is within the Resolution. Not all meters demonstrate the same differences.
It is very important that the right force-indicating instrument is purchased if the end-user wants to perform meter substitution. We have seen so many force-indicating indicators that will not meet the 1/3 requirement, so be careful of what system you may consider. Our Morehouse HADI and Morehouse 4215 for Class AA can meet these requirements.
Does a Backup Load Cell Meter for Your Load Cell System Make Sense? - Conclusion
If the end goal is to minimize risk and not have to send all load cells back for calibration when a meter breaks, the best option is to simply purchase one meter per load cell as it is a one-time cost without any recurring costs.
The next best option is to have a backup load cell meter, which comes with additional costs to perform a further two calibrations, one calibration per meter that will add to the overall calibration fee and will be a recurring cost. Using a single meter per load cell will also help lower uncertainty, while adding a backup or performing substitution will raise the overall uncertainty.
If you enjoyed this article, check out our LinkedIn and YouTube channel for more helpful posts and videos. Elevate your metrology knowledge with our free online training. Sign up here.
If you have additional questions, please contact us at info@mhforce.com. We are here to help you improve your force and torque measurements.
#Backup Load Cell Meter