Load Cell Calibration for Rocket Engine Test Accuracy
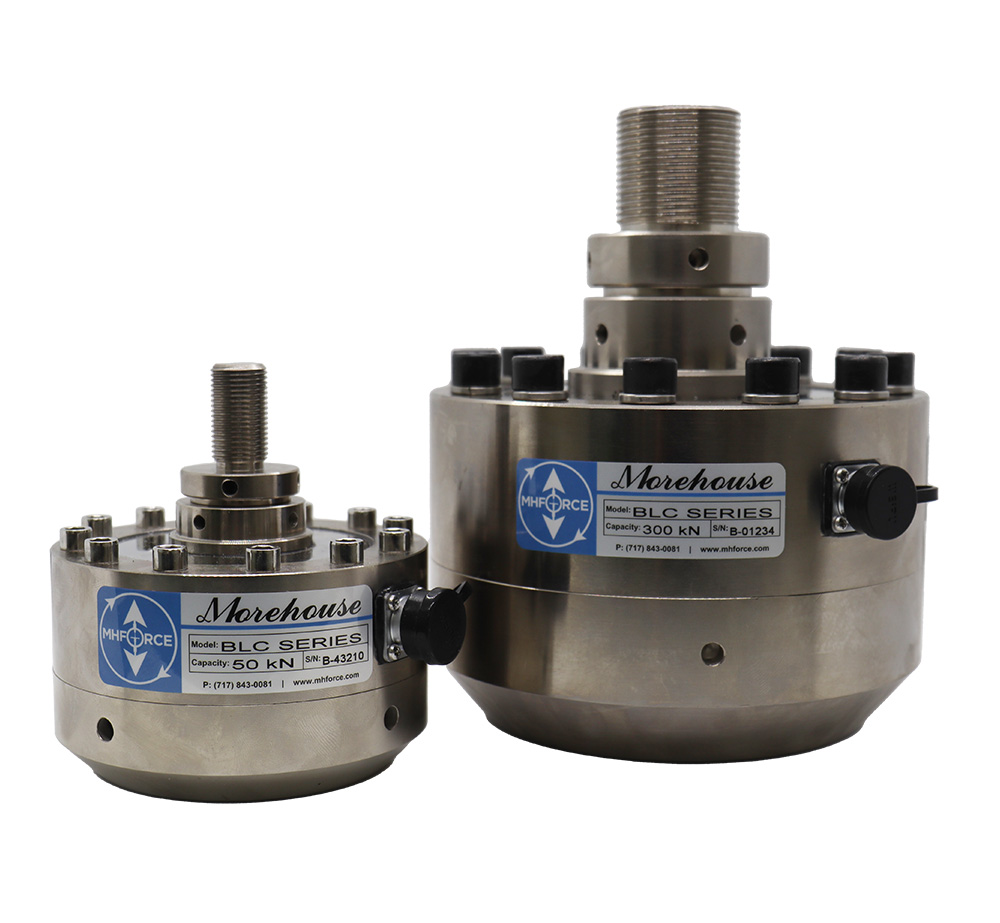
Load cell calibration for rocket engine thrust accuracy is something anyone making rockets should understand.
Rocket engine testing represents one of the most critical phases in aerospace engineering, where precision and reliability are paramount.
This article explores the fundamentals of load cell calibration for rocket engine thrust accuracy and details how load cells measure thrust during static fire tests.
It highlights critical calibration practices, key testing phases, and advancements in modern data acquisition systems to ensure precise and reliable measurements.
However, to elevate the depth and utility of this discussion, several key areas warrant expansion, including emerging technologies in metrology, economic implications of measurement inaccuracies, and comparative analyses with alternative testing methodologies.
This enhanced analysis aims to provide aerospace engineers, project managers, and academic researchers with a holistic perspective on the evolving role of load cells in propulsion system validation.
So, let’s dive deeper into load cell calibration for rocket engine thrust accuracy.
Figure 1 Load cell calibration for rocket engine thrust accuracy setups
1. Fundamental Principles of Thrust Measurement in Rocket Engines
1.1 Mechanical Design of Test Stands
Rocket engines are mounted on rigid test stands designed to work under extreme thermal and mechanical stresses.
Load cells are strategically integrated into these stands at key transmission points to ensure precise load cell calibration for rocket engine thrust accuracy.
Distributing loads and minimizing measurement uncertainty often involve multiple load cells arranged in parallel or series.
A typical setup may employ four orthogonally mounted shear web load cells to capture axial thrust while compensating for lateral forces induced by turbulent exhaust plumes.
The stiffness of the test stand itself significantly impacts measurement accuracy. If the structure is too flexible, harmonic oscillations can be introduced during engine ignition, resulting in signal noise.
Modern test stands incorporate finite element analysis (FEA) during design to optimize performance to refine natural frequency profiles, ensuring they remain outside the engine's operational vibration spectrum.
1.2 Signal Acquisition and Noise Mitigation
Figure 2 Load cell calibration for rocket engine thrust accuracy recommended load cell amplifier.
Raw signals from strain gauges embedded in load cells are susceptible to electromagnetic interference (EMI) from high-voltage ignition systems and turbulent plasma in exhaust streams.
Advanced data acquisition systems now incorporate shielded cabling, differential amplifiers, and adaptive digital filters to suppress noise.
For example, the Morehouse LAC (Load Cell Amplifier and Conditioner) employs proprietary algorithms to isolate thrust signals from ambient vibrations, achieving a signal-to-noise ratio (SNR) of >100 dB.
Note: One problem with most amplifiers is that they are noisy, which impacts the repeatability performance characteristic of the load cell system.
Purchase a standard load cell, such as a Morehouse shear web cell, and pair it with our LAC 65.1 to drastically improve repeatability.
More information on Amplified load cells can be found at https://mhforce.com/amplified-load-cells-4-20ma-0-10-vdc-made-easy/
2. Calibration Traceability and Metrological Challenges
2.1 Primary Calibration Standards
The traceability chain for load cell calibration for rocket engine thrust accuracy begins at national metrology institutes such as NIST, which maintains deadweight machines capable of applying forces up to 4.45 MN.
These primary standards have measurement uncertainties as low as ±0.0005 % of the applied force.
Morehouse uses Primary Standards (deadweight machines) up to 533 kN (120,000 lbf) and is known to ± 0.002 % of applied force.
Secondary calibrations are those which primary standards have calibrated.
These calibrations are performed by accredited laboratories like Morehouse, using hydraulic or pneumatic force multipliers traceable to the SI through an NMI such as NIST.
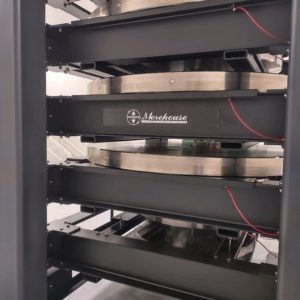
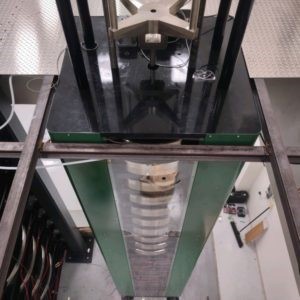
A recent innovation involves the USAF’s adoption of Morehouse’s 453.7 kN deadweight machine. This machine uses stacked precision masses to generate force without relying on hydraulic fluids.
This is the most accurate measurement machine, which can reduce SEB and hysteresis errors by 40 % compared to conventional methods, which is critical for reusable engine testing, where load cells undergo thousands of cycles.
2.2 Environmental Compensation Techniques
Temperature fluctuations during engine tests can induce thermal errors in load cell elements, creating false force readings. Most Morehouse load cells have thermal errors below 0.0008% per degree, representing the best option for test applications.
3. Advanced Applications in Reusable Rocket Systems
3.1 Fatigue Life and Cycle Testing
The rise of reusable launch vehicles like SpaceX’s Falcon 9 demands load cells capable of enduring repeated loading cycles without degradation. Accelerated life testing involves subjecting load cells to tens of millions of cycles without worrying about loadcell failures due to fatigue, creep, drift, and unstable output. Results from such tests have revealed that shear web load cells exhibit superior fatigue resistance compared to bending beam designs, with <0.01% full-scale output drift after 500,000 cycles.
3.2 Thrust Vector Control (TVC) Validation
Load cells are instrumental in validating TVC systems that adjust engine nozzle angles during flight. During testing, engines are gimbaled while under thrust, and multi-axis load cells measure resultant lateral forces. For example, NASA’s RS-25 tests employed a 6-DOF (degree-of-freedom) load cell array to capture forces and moments in all axes, ensuring TVC actuators can compensate for asymmetric thrust profiles.
3.3 Dynamic Modeling
Customers frequently inquire about the dynamic behavior of load cells in test systems. In most cases, the answer is straightforward: a load cell can be modeled as two masses connected by a spring.
By incorporating these elements into the system model, you can assume that the spring’s deflection is directly proportional to the load cell’s output.
For a Morehouse shear web load cell, the output should accurately track this deflection at frequencies exceeding 50 kHz.
Morehouse can provide expert guidance if you need assistance estimating the deflection at full-scale output and the associated mass.
If our standard loadcells do not play well with your system, we can discuss custom loadcells with less weight or stiffer/heavier loadcells made with piezoresistive strain gauge.
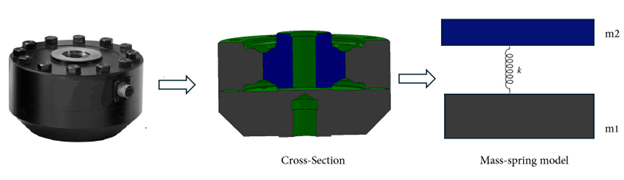
4. Economic and Safety Implications of Measurement Errors
4.1 Cost of Inaccuracy in Payload Optimization
A 1 % error in thrust measurement can lead to a 300 kg overestimation of payload capacity for a medium-lift rocket.
Given launch costs of ~$10,000 per kilogram to low Earth orbit (LEO), such errors risk either forfeiting $3M in potential payload revenue or mission failure due to underperformance.
Load cells calibrated to ±0.05 - 0.1 % uncertainty mitigate this risk, directly enhancing cost efficiency.
4.2 Case Study: Ariane 5 Flight 501 Failure
While not caused by load cell error, the 1996 Ariane 5 disaster underscores the catastrophic consequences of measurement inaccuracies in aerospace systems.
Post-failure analyses led to stricter standards for sensor redundancy and sampling rates, principles now embedded in load cell testing protocols.
Modern systems employ triple modular redundancy (TMR), where three load cells measure the same thrust axis, and a voting logic system discards outliers.
5. Emerging Technologies in Thrust Metrology
5.1 Wireless Load Cells and IoT Integration
Recent advancements include wireless load cells with embedded microprocessors that transmit data via 5G networks.
These sensors eliminate cabling vulnerabilities and enable real-time remote monitoring.
For instance, Blue Origin’s New Glenn test uses wireless load cells with AES-256 encryption to safeguard data integrity during long-duration firings.
5.2 Machine Learning for Predictive Calibration
AI algorithms are trained on historical calibration data to predict load cell drift patterns.
By analyzing temperature, humidity, and cycle count, these models preemptively adjust calibration coefficients and can reduce downtime between manual calibrations by up to 70 %.
6. Comparative Analysis with Alternative Thrust Measurement Methods
6.1 Laser Doppler Vibrometry (LDV)
LDV measures thrust by analyzing vibrations in engine mounts, offering non-contact measurement.
However, its accuracy (±2 %) lags behind load cells, making it unsuitable for precision-critical applications like human-rated launches.
6.2 Piezoelectric Force Plates
Used in short-duration pulse tests (e.g., solid rocket motors), piezoelectric sensors provide high-frequency response yet suffer from charge leakage over time, rendering them ineffective for tests exceeding 60 seconds.
7. Global Standards and Regulatory Frameworks
7.1 FAA and EASA Regulations
The FAA’s 14 CFR Part 33 mandates that engine manufacturers demonstrate thrust measurement systems can detect anomalies leading to ≥5 % deviation from nominal performance. Load cell data must be sampled at ≥1 kHz to capture transient events like pogo oscillations.
7.2 ASTM E74 and ISO 376
Both standards test for the reproducibility condition of the measurement, or what we like to call the expected performance of the load cell when used under similar conditions.
Many will “de-rate” the load cell with different fixturing conditions that drastically vary from the initial calibration, such as temperature.
This is where purchasing a great load cell and monitoring its performance (reliability from one calibration to the next) and performing ANOVA and other statistical tests in the field will help ensure data integrity.
8. Future Directions and Research Opportunities
Conclusion - Load cell calibration for rocket engine thrust accuracy.
The role of load cells in rocket engine testing transcends mere force measurement—it is the linchpin ensuring mission success, cost efficiency, and technological advancement in aerospace. As reusable rockets and deep-space propulsion systems evolve, load cell technology must parallel these strides through innovations in wireless connectivity, AI-driven calibration, and nanotechnology.
Organizations investing in metrological rigor, such as Morehouse’s precision deadweight machines, will remain at the vanguard of this critical field, enabling humanity’s sustainable expansion into space.
Enhancing Load Cell Calibration for Rocket Engine Thrust Accuracy
Future research should prioritize harmonizing calibration standards globally to ensure consistency across international aerospace programs. Additionally, integrating quantum sensor technology could revolutionize thrust measurement by achieving unprecedented precision and fidelity in force calibration.
Ensuring Load Cell Calibration for Rocket Engine Thrust Accuracy with Reliable Calibration and Cost Savings with Morehouse
Accurate thrust measurement is essential for rocket engine testing, as even minor miscalculations can lead to mission failure or excessive costs.
As reusable rockets and deep-space propulsion systems evolve, load cell technology must parallel these strides through innovations in wireless connectivity and AI-driven calibration.
By utilizing Morehouse load cells and their industry-leading calibration standards, organizations can ensure measurement confidence with traceable and repeatable force measurements.
Morehouse’s advanced deadweight calibration machines provide unparalleled precision, minimizing measurement uncertainty and improving test reliability.
Investing in a properly calibrated load cells enhances data accuracy and helps save money by reducing errors, optimizing fuel efficiency, and ensuring successful launches.
With each pound of payload costing approximately $10,000 to send into space, precise thrust measurement is critical.
Partnering with Morehouse guarantees the right load cell(s) are provided with superior calibration, reliable data, and cost-effective rocket testing, ultimately contributing to safer and more successful space missions.
More Information about Morehouse
We believe in changing how people think about Force and Torque calibration in everything we do. That includes discussions on Load cell calibration for rocket engine thrust accuracy.
This includes setting expectations and challenging the "just calibrate it" mentality by educating our customers on what matters and what may cause significant errors.
We focus on reducing these errors and making our products simple and user-friendly.
This means your instruments will pass calibration more often and produce more precise measurements, giving you the confidence to focus on your business.
Companies around the globe rely on Morehouse for accuracy and speed.
Our measurement uncertainties are 10-50 times lower than the competition, providing you with more accuracy and precision in force measurement.
We turn around your equipment in 7-10 business days so you can return to work quickly and save money.
When you choose Morehouse, you're not just paying for a calibration service or a load cell.
You're investing in peace of mind, knowing your equipment is calibrated accurately and on time.
Through Great People, Great Leaders, and Great Equipment, we empower organizations to make Better Measurements that enhance quality, reduce risk, and drive innovation.
With over a century of experience, we're committed to raising industry standards, fostering collaboration, and delivering exceptional calibration solutions that build a safer, more accurate future.
Contact Morehouse at info@mhforce.com to learn more about our calibration services and load cell products.
Email us if you ever want to chat or have questions about a blog.
We love talking about this stuff. We have many more topics other than expressing SI units!
Our YouTube channel has videos on various force and torque calibration topics here.
# Load cell calibration for rocket engine thrust accuracy