Tension Links: Are Your Measurements Accurate?
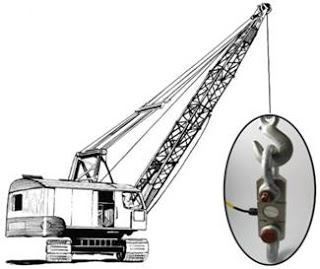
You are out in the field with a tension link, load link, or some type of digital dynamometer to use for a weighing application. You need pins to engage into the unit. What can you use? Slings? Maybe one size pin with one diameter on one end and another pin with a different diameter on the other end. As long as the fixtures are safe to hold the load it shouldn’t matter, should it?
Tension Link Pin Size is Critical
Tension Link Loaded Without The Proper Pin Size
Here at Morehouse, we have done testing this issue in mind. Forged pins, for example, can differ by small amounts in diameter from pin to pin. Depending on the Scale manufacturer, we have seen differences up to 1.7% between different sets of pins (The picture above and below demonstrate this). If your instrument has an accuracy of 0.1%, your error could be 17 times greater by substituting pins.
Tension Link Loaded with Proper Pin Size
Calibration should be performed with the same load pins the end-user is using the device. Some links exhibit very high errors when substituting different types of pins.
Attention:
It is important to position any forged loading pins through the shackles the same way that we had the pins positioned during our calibration. There can be variations in the surface of the pins from one pin to the next. This variation may affect your ability to reproduce the calibration results. We have a standard practice to label the pins. Standard practice is to label the TOP PIN, and BOTTOM PIN, and mark the direction of each pin with an up arrow at the 12:00 position. This helps the end user eliminate as much variation as possible, allowing for reproducible measurements.
Tension Links Good Measurement Practice
- Using correctly sized pins is critical
- Do not use pins that are worn or bent
- If links are damaged, highly used, or worn, decrease the time between calibrations
- The same size and style of shackle and pin used during operation should be used for calibration
- Maintaining pin orientation is the best practice
When the end-user does not send in an adapter, the calibration laboratory is left with having to load the device with some pin. Luckily Morehouse has developed Clevis Kits to solve this problem.
Figure 1: Manufacturer's specification sheet for tension links
Finding the right pin size can be tricky as shown in Figure 1 as the manufacturer’s recommendations may be counter-intuitive. In Figure 1 example, a 20-ton tension link requires a 2.0-inch pin, and a 25-ton requires a 1.97 (50mm) pin. One may say 0.03 inches will not make a difference and we would say go ahead and test it. On a device with an accuracy specification of 0.1 % of full scale, we have observed a change of 0.03 inches to use up 70 % of that specification.
Figure 2: Morehouse Clevis Kits to Calibrate Tension Links
Knowing these issues, Morehouse has designed clevis assemblies for use with our Quick-Change Tension Adapters. These assemblies cross-reference the manufacturer’s recommended pin size and allow the calibration laboratory to calibrate hundreds of tension links, crane scales, dynamometers, and rod-end load cells all with using the same clevis. Not only does this simplify the logistics of having the proper adapter, but it improves cycle time and standardizes the calibration process. Morehouse Clevis kits.
Figure 3: 1 of 3 pages of model numbers the Morehouse Adaptable Clevis Kits can be used to calibrate a tension link
Tension Links: Are your measurements accurate? - Conclusion
I take great pride in our knowledgeable team at Morehouse, who continue to work with everyone, clarify complex topics, and provide tools such as free guidance documents, excel sheets, and products to help you make better force measurements. We want to make sure everyone knows what makes great equipment used to measure force.
At Morehouse, we educate our customers and provide solutions to you. Most of these solutions are available for free to help you make better measurements and can be found here.
We have been in business for over a century and focus on being the most recognized name in the force sensor calibration business. That vision comes from educating our customers on what matters most and having the proper discussions relating to the calibration of a tension link.
If you enjoyed this article, check out our LinkedIn and YouTube channel for more helpful posts and videos.
Everything we do, we believe in changing how people think about force and torque calibration. We challenge the "just calibrate it" mentality by educating our customers on what matters, what causes significant errors, and how to focus on reducing them. I
n addition, Morehouse makes simple-to-use calibration products. We build excellent force equipment that is plumb, level, square, and rigid.
If you have more questions about what is a load cell, or other questions, don't hesitate to get in touch with us @ 717-843-0081 to talk to a live person or email info@mhforce.com. Visit us on the web at mhforce.com.